Kala saarista PCB waxay u horseedi kartaa arrimo waxqabad oo la taaban karo, gaar ahaan naqshadaha qallafsan ee adag halkaasoo la isku daray walxaha adag iyo kuwa dabacsan. Fahamka sida looga hortago delamination ayaa muhiim u ah hubinta cimriga dheer iyo isku halaynta shirarkan adag. Maqaalkani waxa uu sahamin doonaa tabo wax ku ool ah si looga hortago delamination PCB, diirada saaraya PCB lamination, waafaqid alaabta, iyo hagaajinta cabbirada machining.
Fahamka Delamination PCB
Delamination waxay dhacdaa marka lakabyada PCB ay kala soocaan arrimo kala duwan, oo ay ku jiraan diiqada kulaylka, nuugista qoyaanka, iyo cadaadiska farsamada. PCB-yada qallafsan, caqabada waa la kordhiyey sababtoo ah sifooyinka kala duwan ee qalabka adag iyo kuwa dabacsan. Sidaa darteed, hubinta iswaafajinta udhaxeysa agabkan ayaa ah tillaabada ugu horeysa ee ka hortagga delamination.
Hubi Waafaqsanaanta Qalabka PCB
Doorashada agabku waxay muhiim u tahay ka hortagga delamination. Marka la naqshadeynayo PCB-gacan-fudud, waxaa lama huraan ah in la doorto agabka leh isku-xireyaasha ballaarinta kulaylka oo isku mid ah. Waafaqidni waxa ay yaraynaysaa diiqada inta lagu jiro baaskiil wadida kulaylka, taas oo keeni karta delamination. Intaa waxaa dheer, ka fiirso xabagta loo isticmaalo habka lamination. Xabag tayo sare leh oo si gaar ah loogu talagalay codsiyada qallafsan ayaa si weyn u wanaajin kara xoogga isku xidhka ee u dhexeeya lakabyada.
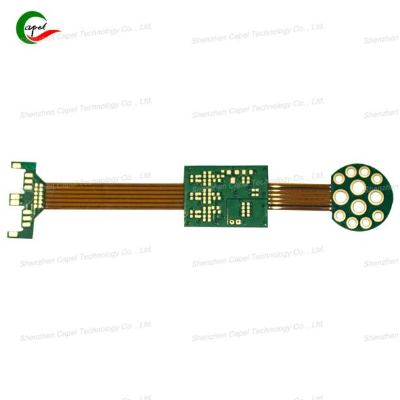
Habka Lamination PCB
Habka lamination waa marxalad muhiim u ah wax soo saarka PCB. Lamination saxda ah waxay hubisaa in lakabyadu si fiican isugu dhejiyaan midba midka kale, yaraynta khatarta delamination. Waa kuwan qaar ka mid ah talooyin wax ku ool ah oo loogu talagalay daahitaanka PCB ee waxtarka leh:
Xakamaynta heerkulka iyo cadaadiska: Hubi in habka lamination lagu sameeyo heerkulka saxda ah iyo cadaadiska. Heerkulka aadka u sarreeya ayaa hoos u dhigi kara alaabta, halka cadaadiska aan ku filnayn uu keeni karo dhejis xumo.
Vacuum Lamination: Isticmaalka faakuumka inta lagu jiro habka shaandhaynta waxay kaa caawin kartaa baabi'inta xumbo-xumada taasoo keeni karta dhibco daciif ah curaarta. Farsamadan waxa ay hubisaa in cadaadis isku mid ah uu ka socdo lakabyada PCB-ga.
Waqtiga DaawayntaU ogolow wakhti daaweyn ku filan si ay koollada si sax ah isugu xidho. Ku degdegista habkani wuxuu u horseedi karaa ku-dhejin aan dhamaystirnayn, kordhinta khatarta delamination.
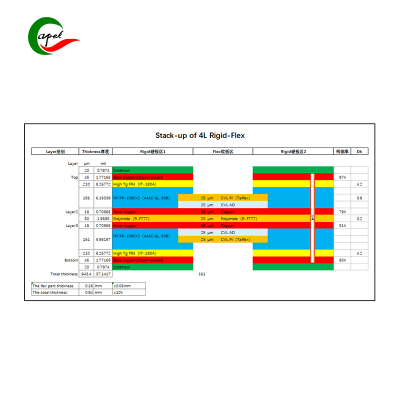
Hababka Mashiinka PCB ee Adag-Flex La Habeeyay
Halbeegyada mishiinadu waxay door muhiim ah ka ciyaaraan daacadnimada PCB-yada dabacsan. Waa kuwan qaar ka mid ah talooyinka mashiinka la hagaajiyay si looga hortago delamination:
Farsamooyinka qodistaIsticmaal xawaare ku haboon iyo xawaarihiisa si aad u yarayso kulaylka inta lagu jiro habka qodista. Kulaylka xad-dhaafka ah wuxuu wiiqi karaa isku-xidhka xabagta wuxuuna horseedaa delamination.
Jideynta iyo Goynta: Markaad waddo marinayso ama goynayso PCB-ga, hubi in qalabku fiiqan yahay oo si wanaagsan loo ilaaliyo. Qalab caajis ah ayaa sababi kara cadaadis iyo kulayl xad dhaaf ah, taasoo wax u dhimaysa daacadnimada lakabyada.
Daawaynta Cidhifka: Si habboon u daawee cidhifyada PCB ka dib marka aad mishiinka samayso. Tani waxay ku lug yeelan kartaa silcin ama xidhid cidhifyada si looga hortago qoyaanka soo galaya, taas oo gacan ka geysan karta delamination waqti ka dib.
Talooyin wax ku ool ah oo looga hortagayo kala saarida PCB
Marka lagu daro xeeladaha kor ku xusan, tixgeli talooyinka wax ku oolka ah ee soo socda:
Xakamaynta DeegaankaKu kaydi PCB-yada deegaan la xakameeyey si aad uga hortagto nuugista qoyaanka. Qoyaanka wuxuu daciifin karaa isku-xidhka xabagta wuxuuna u horseedi karaa delamination.
Tijaabada Joogtada ahHirgelinta baaritaanka joogtada ah ee PCB-yada calaamadaha delamination inta lagu jiro habka wax soo saarka. Ogaanshaha hore waxa ay kaa caawin kartaa yaraynta arrimaha ka hor inta aanay sii xumaan.
Tababarka iyo Wacyigelinta: Hubi in dhammaan shaqaalaha ku lug leh habka wax soo saarka PCB lagu tababaro hababka ugu fiican ee lamination iyo mashiinada. Ogaanshaha arrimaha ka qaybqaata delamination waxay horseedi kartaa go'aan-qaadasho wanaagsan.
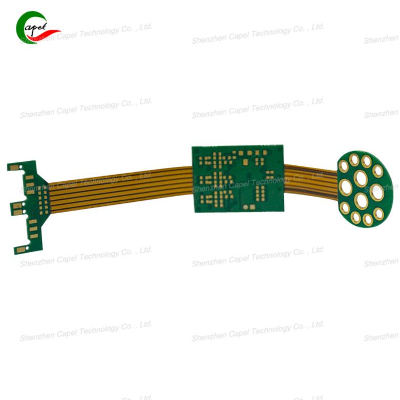
Waqtiga boostada: Oct-31-2024
Dib u noqo